MBD (Module Base Design) White Paper Plug-Play & Turnkey
Standard Interface & Module enhance Equipment Extendability & Maintanance.
By 2025, deliver GMP-compliant plug-and-play modules with ≤1% CV uniformity across 80℃–120℃ zones – eliminating product variance in herb/spice drying.
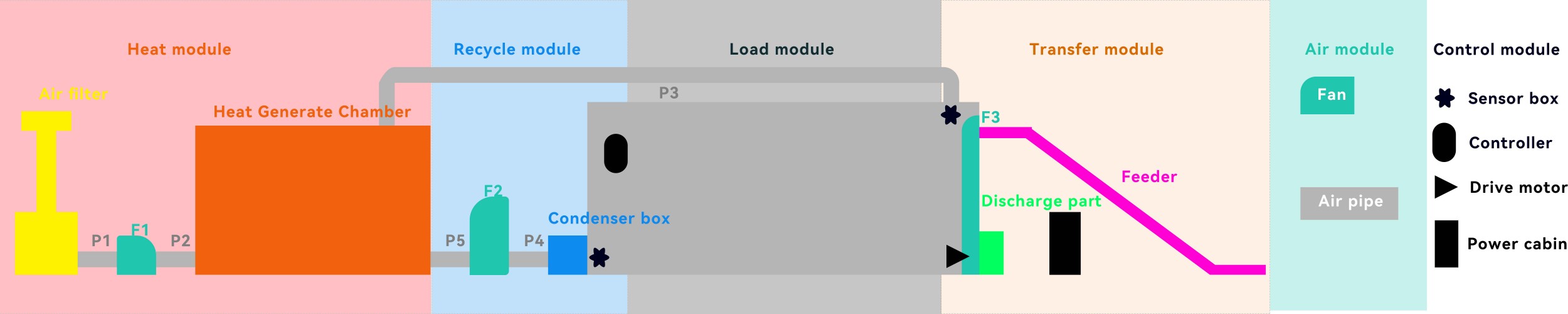