Easy Use of Starch Extractor -
Instruction
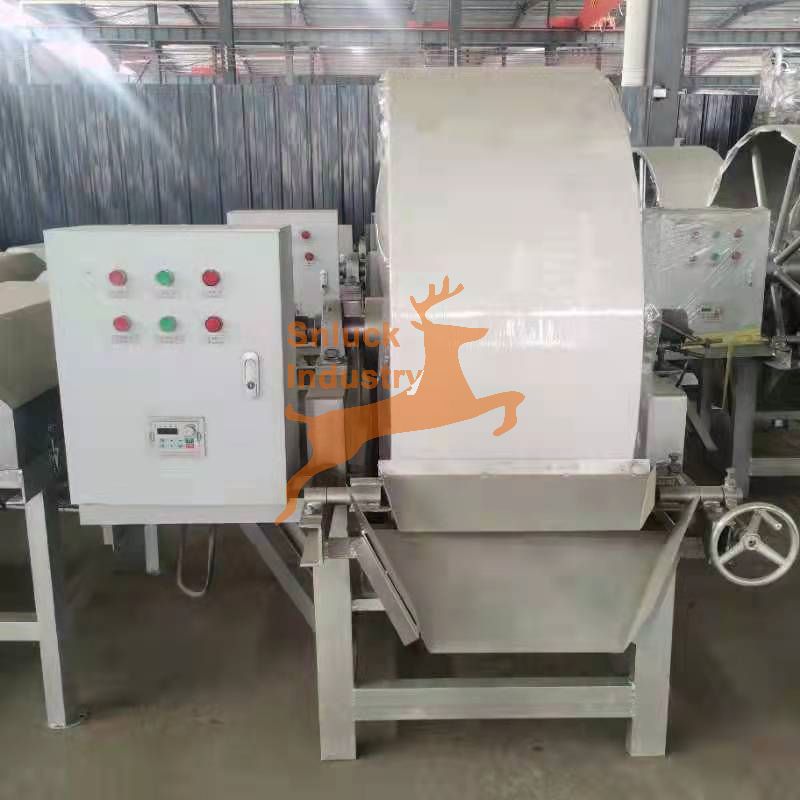
- 1Equipment Inspection – Thoroughly examine the exterior of the vacuum drum – type filter for any signs of damage, loose parts, or abnormal wear. Pay special attention to the hollow drum, shaft air system, transmission device, and stirring device.
- 2Cleaning – Clean the interior and exterior of the equipment, including the hollow drum, filter cloth, and slurry tank. Remove any residual materials from previous operations to prevent contamination of the new batch.
- 3Filter Cloth Installation and Adjustment – Install a new or clean filter cloth on the surface of the hollow drum. Make sure it is properly seated and evenly tensioned.
- 4Material Preparation – Prepare the slurry according to the production requirements. Ensure the particle size and concentration of the slurry are within the appropriate range for the vacuum drum – type filter.
- 5Start the stirring device in the slurry tank to keep the slurry in a uniform state.
- 6The discharged filter cake is collected in a designated container for further processing or packaging.
- 7Clean the hollow drum, filter cloth, and slurry tank again to remove any remaining filter cake and slurry residues.